ENGINEERINGNET.BE - Cet article vous montrera comment une alliance entre l’IA, la technologie des puces et le monde des connaissances est à même de transformer ces processus.
Un contrôle précis de la qualité et des processus s’avère primordial pour améliorer l'efficacité de ces processus de production. À cet égard, la collecte de données et de connaissances adéquates est cruciale. À titre d’exemple, la biofabrication est confrontée à divers défis tels que la production biologique de cellules humaines dans le cadre de la thérapie par cellules souches ou CAR-T.
Ce processus à délai critique se caractérise par la grande sensibilité du produit fini à la moindre variation affectant le processus. C’est pourquoi la maîtrise traditionnelle des processus comprend souvent une surveillance ‘hors ligne’ qui consiste à prélever des échantillons dans le flux de production aux fins d’analyse plus poussée. Ces mesures livrent des indications quant à la qualité du produit actuel ainsi que des informations intéressantes pour les productions ultérieures; mais en dépit de l’investissement temporel et financier, elles ne permettent pas de corriger le processus actuel.
Scénario idéal: une surveillance ‘en ligne’ comportant une évaluation et une rectification en temps réel, voire automatiques, des mécanismes sous-jacents. Une telle surveillance se traduirait non seulement par une réduction des coûts et du temps de production global, mais aussi par une baisse de la consommation d’énergie et de matières premières ainsi que, le cas échéant, par une amélioration de la qualité du produit fini.
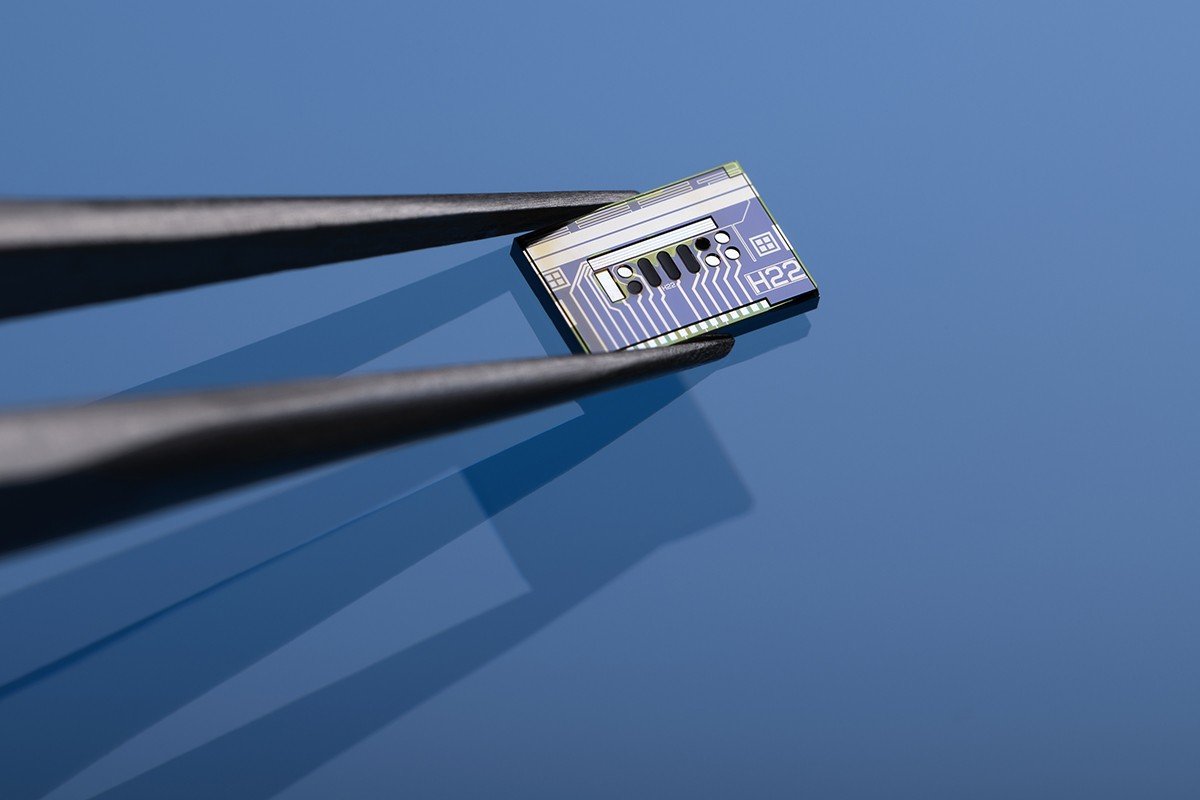
Surveillance en ligne reposant sur la technologie des puces
«L’apparition de capteurs de surveillance en ligne tels que les sondes de mesure du pH et de la température au sein d’un bioréacteur remonte à plus de 40 ans. Mais pour mesurer tous les paramètres pertinents, il faut disposer d’une foule de sondes et dispositifs hors ligne dont la présence pose divers problèmes d’installation, d’étalonnage, de traitement des données et même de stérilisation. Notre expertise en technologie des puces nous a permis de miniaturiser divers capteurs en ligne et de les intégrer au sein d’une seule sonde, en remédiant ainsi à ces multiples problèmes», relate Bert Verbruggen, directeur de programme auprès de l’imec.
Concrètement, les chercheurs de l’imec ont développé, sous forme de sonde, un capteur reposant sur une technologie d’analyse de processus (PAT). Ce capteur intégré, miniaturisé et multiparamétrique procède simultanément et en temps réel à la mesure de paramètres essentiels tels que la température, l’oxygène dissous, la conductivité électrique, la concentration en glucose, la teneur en lactates et même la densité cellulaire, au sein d’un bioréacteur par exemple. Lors d’une phase ultérieure, les chercheurs entendent rallonger la durée des mesures (deux semaines aujourd’hui) et développer un ‘système en boucle fermée’ dans lequel toute rectification des processus de production s’opérera automatiquement en fonction de mesures intermédiaires.
Rôle de l’IA dans la compréhension de la complexité des processus
S’il faut impérativement disposer de quantités considérables de données de mesure, c’est parce que la complexité appréciable des processus (bio)chimiques en rend la prévisibilité plus ardue. Dès lors, le développement de modèles évolués autorisant l’intégration transparente de mesures en ligne avec des données historiques et des modèles spécifiques est une nécessité. L’IA nous permet d’élaborer des prévisions détaillées concernant certaines caractéristiques de qualité critiques (CQF), telles que le pourcentage de protéines correctement repliées dans les produits pharmaceutiques.
La mesure directe des paramètres de cette nature s’avère souvent difficile; mais grâce à l’IA leur prévisibilité se caractérise par un haut degré de certitude. Cette approche a été testée dans le cadre du projet Catalisti DAP2CHEM. Des chercheurs anversois de l’IDLab, un groupe de recherche imec associé à l’UAntwerpen et à l’UGent, ont élaboré une plateforme de simulation numérique d’une ‘usine pilote de développement chimique’ en collaboration avec la KU Leuven et Johnson & Johnson.
L’intégration à cette fin d’un modeste ensemble de données issues de mesures de processus avec certaines connaissances spécifiques s’est traduite par la réalisation d’un modèle de simulation hybride et d’un modèle d’optimisation basé sur un ‘apprentissage par renforcement profond’. Ce modèle a permis l’exécution de milliers d'expériences virtuelles - une somme dont on ne peut que rêver au niveau de l’usine. Résultat: une recette optimisée permettant de réduire de plus de 30% les durées et les coûts ainsi que la quantité de solvant requise.
En outre, cette approche s’est traduite par une réduction de la production de déchets, l’obtention d’un produit fini plus pur et la réalisation d’économies d'énergie supérieures à 10%. Siegfried Mercelis de l’IDLab Antwerpen: «Dans le cadre de ce projet, nous avons démontré que les innovations basées sur l’IA ne doivent pas se limiter à des concepts théoriques et qu’elles se prêtent à la création de valeur considérable, même à partir d’une quantité limitée de données.
L’intégration progressive de capteurs sophistiqués dans le processus réduit la nécessité d'une modélisation complexe et chronophage et accroît l’extensibilité de la technologie pilotée par l’IA. La conjugaison de l’expertise acquise dans le domaine du matériel et de l’IA ouvre de nouvelles perspectives d’optimisation significatives dans le cadre de processus allant de la biofabrication à la production d’aliments.»
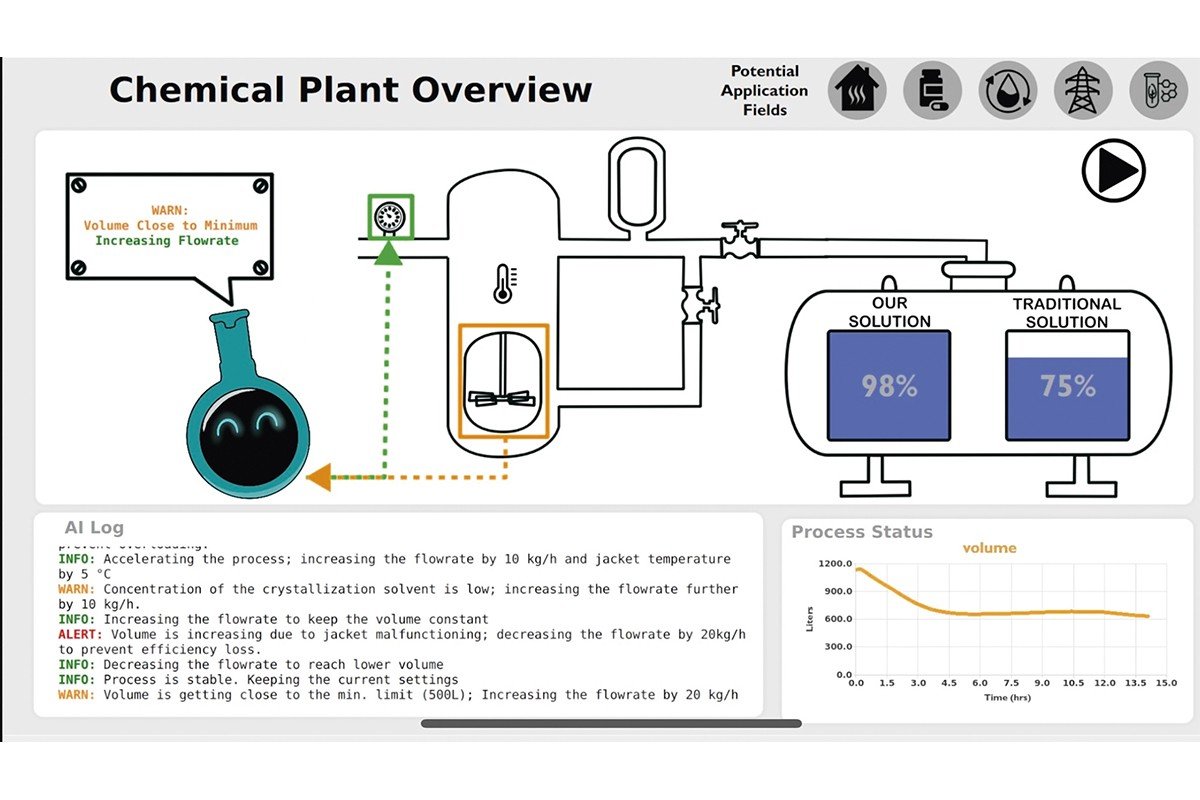
Du modèle mystérieux à l’enseignement
Si, en dépit d’avantages indéniables, la mise en oeuvre de l’IA dans l’industrie demeure limitée pour le moment, c’est en partie à sa nature de ‘boîte noire’ qu’elle le doit. C’est pourquoi les chercheurs imec associés au projet DAP2CHEM sont allés plus loin et ont développé un modèle transparent piloté par une IA explicable (XAI), laquelle éclaire de manière intelligible le déroulement des processus de prise de décision.
Ce modèle suscite la confiance des opérateurs humains envers cette technologie et facilite l’interaction avec celle-ci. En effet, non content de trouver de nouvelles recettes, le modèle d’optimisation est également à même de procéder, en temps réel, au contrôle et à l’optimisation de processus. Par ailleurs, outre la simple diffusion d’informations, le modèle d’IA est également à même de former en partie les opérateurs.
C’est précisément l’objectif sur lequel le projet imec.icon CHAI s’est focalisé ces dernières années: une collaboration entre un certain nombre de partenaires industriels et les IDLab de Gand et d’Anvers dans le cadre de laquelle seront conçus des algorithmes XAI hybrides. Les processus de production ont bénéficié d’une optimisation poussée dans deux cas pratiques distincts: production de résines (Allnex Belgium) et fabrication d’assouplissants (Procter & Gamble).
Les résultats positifs d’une mise en oeuvre amorcée en laboratoire ont été extrapolés vers l’environnement de production. Chez allnex, par exemple, la surveillance traditionnelle a bénéficié de l’adjonction de modèles prédictifs. Ces modèles tiennent compte de réactions chimiques éventuelles. Outre la mise en évidence de l’état actuel du processus de réaction, ces modèles permettent de prédire les caractéristiques du produit fini.
Ainsi, les opérateurs savent précisément à quel moment intervenir. Pour ce qui concerne Procter & Gamble, il s’agissait de rendre la stabilité des nouveaux produits plus prévisible afin d’en accélérer la commercialisation.
L’optimisation contextuelle ne se résume pas à l’exécution de mesures
Le consortium CHAI a également inversé les rôles: comment le modèle d’IA peut-il se nourrir de l’expertise des opérateurs - et comment l’intégrer sans discontinuer dans notre modèle ? Des experts/opérateurs ont été invités à contextualiser certaines informations émanant de capteurs et à mettre en lumière les liens existants entre les processus de production et diverses valeurs mesurées, telles que la température ou la viscosité.
Cette approche structurée permet au modèle d’IA de poursuivre son apprentissage sur la base des données saisies et de l’expérience sous-jacente de l’informateur. Elle permet également au modèle de faire preuve de souplesse face à l’ambiguïté des opinions et d’apprendre à résoudre les conflits d’opinion entre les opérateurs. Michaël Rademaker de l’IDLab Gent, insiste: «Nous observons qu’à l’heure actuelle, le pilotage d’un processus (bio)chimique est encore limité par les données et les connaissances.
Après l’identification des étapes critiques du processus, nous avons pu tester et valider l’optimisation pilotée par l’IA, expertise humaine à l’appui. Notre collaboration avec plusieurs partenaires industriels s’est d’ailleurs traduite par un enrichissement mutuel dans plusieurs domaines. De plus, nos partenaires industriels sont également aux premières loges quant au développement de l’optimisation des processus.»
Ces projets marquent un changement de paradigme dans une industrie (bio)chimique où la synergie entre matériels, connaissances humaines et IA favorise l’émergence de processus plus efficaces, moins gaspilleurs et doués d’un potentiel d’innovation inédit. «Mesurer, c’est encore et toujours savoir, surtout si les mesures effectuées sont enrichies par les connaissances d’experts à même de les resituer dans un contexte plus large. Nos projets démontrent donc que, grâce à la puissance de l’IA hybride, 1 + 1 peut être égal à 3», conclut Rademaker.
CHAI est un projet de recherche imec.icon financé par imec et l’Agentschap Innoveren & Ondernemen (VLAIO) qui devrait prendre fin en mars 2024. Le consortium CHAI se compose des partenaires industriels allnex Belgium, Dotdash, Procter & Gamble Services Company ainsi que des centres de recherche IDLab Data Science Lab (UGent), IDLab IBCN (UGent) et IDLab MOSAIC (UAntwerpen).
DAP2CHEM est un projet d’innovation sous l’égide de Catalisti, le cluster de pointe qui accélère l’innovation commerciale dans le secteur de la chimie et des matières synthétiques en Flandre. Ce projet soutenu par la Vlaamse Agentschap Innoveren & Ondernemen (VLAIO) a pris fin en septembre 2022. Le consortium DAP2CHEM se composait des partenaires suivants: imec, KU Leuven, Flanders Make, Ajinomoto OmniChem, Cronos Group, Johnson & Johnson (Janssen Belgium) et Procter & Gamble Services Company.