ENGINEERINGNET.BE - À ce stade-ci, la fermeture de la boucle circulaire de certains flux plastiques était impossible. Le recyclage mécanique était possible, mais la purification exigée manquait pour un soi-disant ‘recyclage avancé’. « Pour les plastiques, la solution du recyclage chimique est une drop-in feedstock au moins comparable à la matière première fossile originelle. »
Depuis octobre, Indaver érige sur son site d'Anvers une installation de dépolymérisation des déchets plastiques (ménagers) (PS et PO) pour les réduire à nouveau en monomères. « Dans un premier temps, l'usine pilote, qui sera située sur un site de 6.000 m², réalisera des campagnes distinctes pour le PS et le PO », explique Moerman.
En 2027, la ligne passera à l'industrialisation et sera étendue à 65.000 tonnes/an pour ne traiter que le PS. L’investissement total est d'environ 100 millions d'euros. Indaver reçoit pour le projet 7,5 millions d'euros d'aide du gouvernement flamand et 3 millions d'euros d'aide via le Flanders Recycling Hub. En parallèle, le projet P2C planifie une usine qui ‘recyclera’ les polyoléfines à partir de 2027.
Le PS et le PO se dépolymérisent
Le PS est dépolymérisé en huile de styrène ; cette dernière devient du r-styrène (styrène recyclé) après purification. Ce dernier est livré avec un label qualité de garantie. « Classe ASTM. Le PS qui peut être créé avec ce dernier peut donc par exemple également être utilisé pour des applications en contact avec des aliments. » Le choix a été fait pour du drop-in feedstock.
Après sa polymérisation, des granulés peuvent être livrés sous la forme et le format exigés par le client/marché. La dépolymérisation du PO donne du naphta brut qui devient du r-naphta (naphta recyclé) après purification. Ce dernier est converti dans le vapocraqueur en nouvelles oléfines avec lesquelles des polyoléfines peuvent être produites. Le cycle PS est plus restreint/plus court que celui des polyoléfines « mais il y a plus de polyoléfines que de PS », stipule Moerman.
Ligne 1, Ligne 2, Ligne 3
La ligne pilote, qui démarrera en Q1-2024, mènera des campagnes distinctes (PS ou PO) jusqu'au début de 2027. Le passage d'une campagne à l'autre est drastique. Il s'agit bien de chaînes d'approvisionnement assez complexes. Un stockage intermédiaire est nécessaire lors de la fourniture des matériaux. Les installations doivent être nettoyées entre chaque campagne.
« Nous voulions gérer la première usine de cette façon », déclare Moerman, « après cela, nous passerons à des usines plus spécialisées. » Au départ, cependant, l'on voulait démontrer que l'ensemble de la technologie fonctionne aussi à grande échelle pour les deux flux de plastique. L'apprentissage et l'acquisition d'enseignements sont les buts de l'usine pilote. L'alternative était de construire de toutes pièces deux usines spécialisées. L'usine pilote (ligne 1) aura une capacité de traitement de 26.000 tonnes/an.
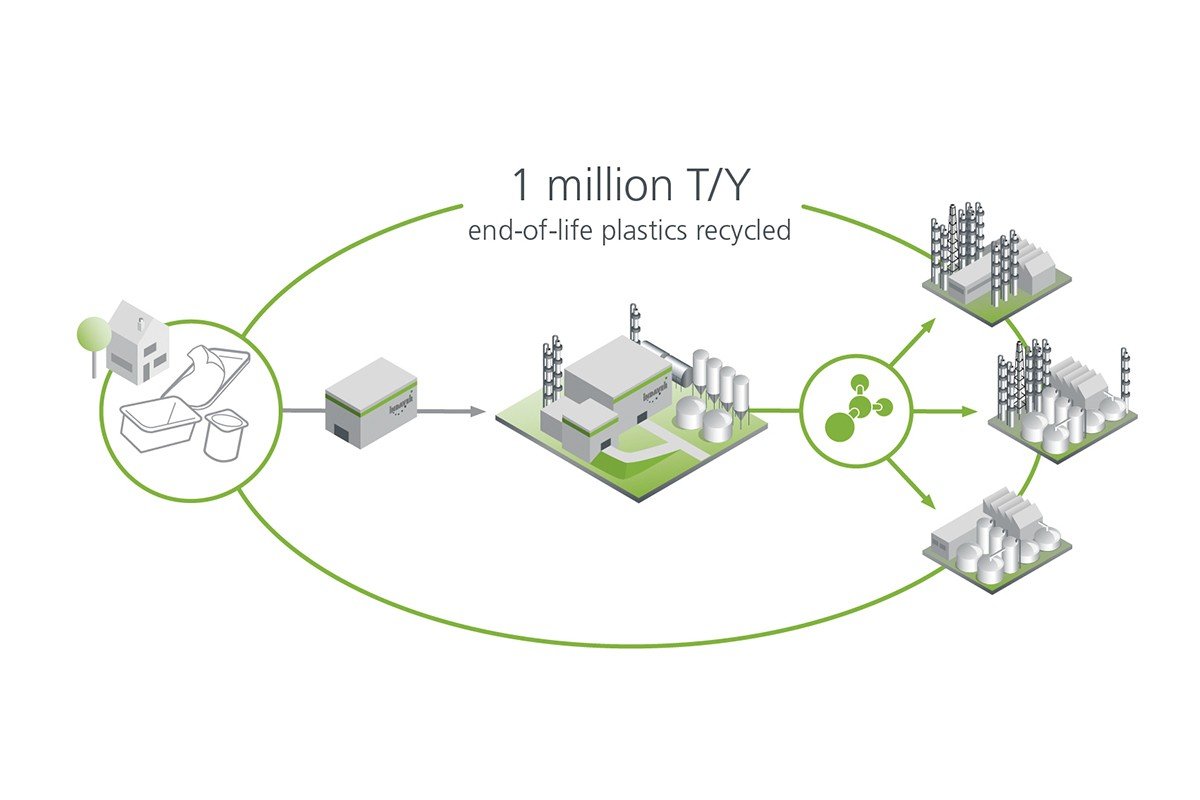
Début 2027, les campagnes alternatives seront terminées et cette ligne basculera entièrement sur le traitement PS. L'usine de PS est constituée d'une extrudeuse qui alimente un réacteur ; ensuite, la matière est condensée et fractionnée. Le produit final envisagé est du PS d'une pureté de 99,7%. Entre-temps, la ligne 2 est en conception en tant que prolongement de la ligne 1.
Indaver attend le feu vert pour cette dernière en 2025. Seront installés plus tard un réacteur supplémentaire, une seconde extrudeuse, un espace de stockage … qui incrémenteront la capacité à 39.000 tonnes/an de PS. Le feu vert est également attendu en 2025 pour une nouvelle usine capable de traiter jusqu'à 50.000 tonnes/an de PO. « L'emplacement exact n'a pas encore été déterminé », avoue Moerman. Une étude de faisabilité devrait apporter plus de clarté d'ici cet été.
L'approvisionnement en déchets
Un prérequis exigé est que l'usine puisse s'accommoder de ‘déchets’. La solution choisie par Indaver est de se reposer sur les flux de déchets existants et de les purifier en interne. De cette manière, la qualité de son produit final sera identique à celle du styrène extrait de matières premières fossiles. « Nous nous concentrons sur les spécifications de nos contrats d'achat. »
La nouvelle station de tri d'Indaver à Willebroek a démarré en décembre 2020 ; elle trie quelques 20 tonnes de déchets ménagers PMC à l'heure en quatorze fractions différentes. Avec deux équipes, la production s'élève à 65.000 tonnes de déchets PMC par an. Depuis le démarrage de la nouvelle usine de tri, 30 millions d'euros supplémentaires ont été investis pour prétraiter le plastique trié. C'est-à-dire broyer, laver, sécher et agglomérer. « La matière passe dans une presse et le produit final se décline en grains ou en pellets (agglomérat). »
Le PS et le PO triés sont prétraités sur deux lignes distinctes pour être transformés en agglomérat. Ce matériau entre en stockage intermédiaire dans des silos ; le transfert se fait sur demande à l'usine d'Indaver recyclant chimiquement. Cet agglomérat final sera stocké là dans six silos. De là, il est transféré à l'extrudeuse ; elle transforme le matériau sous pression et à température en une masse fondue qui est pyrolysée.
S'ensuit une distillation dans deux tours de distillation de 40 m de haut. Si exigé, un nettoyage extra est possible. Les produits intermédiaires et finis (sous forme liquide) seront emmagasinés dans un parc de stockage. Le transport se fait en première instance par camion. Les fractions gazeuses non condensables et plus légères se libérant à des températures plus élevées seront réorientées directement vers la centrale électrique pour produire de la vapeur pour les process de distillation et la production d'électricité.
Fournisseurs et acheteurs
Les négociations avec les partenaires potentiels sont en cours depuis 2017. L'approvisionnement pour les trois premières années est entre-temps déjà organisé. L'usine recevra les déchets d'emballages ménagers triés de l'usine d'Indaver à Willebroek. « Nous avons également obtenu 80% de tous les PS qui sont triés en France par Citeo, plus ou moins le pendant français de FostPlus », souligne Moerman.
Le contrat de fourniture est valable neuf ans. Les acheteurs sont également largement connus aujourd'hui. Le styrène récupéré est livré moitié-moitié chez INEOS Styrolution et Trinseo. Les produits r-styrène et r-PS seront certifiés bilan massique ISCC Plus. Le naphta produit est destiné à différents clients dont Total Energies notamment.
Demande importante
« La demande pour ce type de produits est supérieure à l'offre », déclare Moerman. Cela aide au décollage de cette nouvelle technologie. L'évolution du prix à long terme est encore incertaine. Cependant, avec la législation attendue relative au recycled content et la nécessaire réduction des émissions de CO2, la demande devrait probablement rester supérieure à l'offre au cours des dix prochaines années.
« En premier lieu, notre objectif est de réussir le parcours circulaire. »
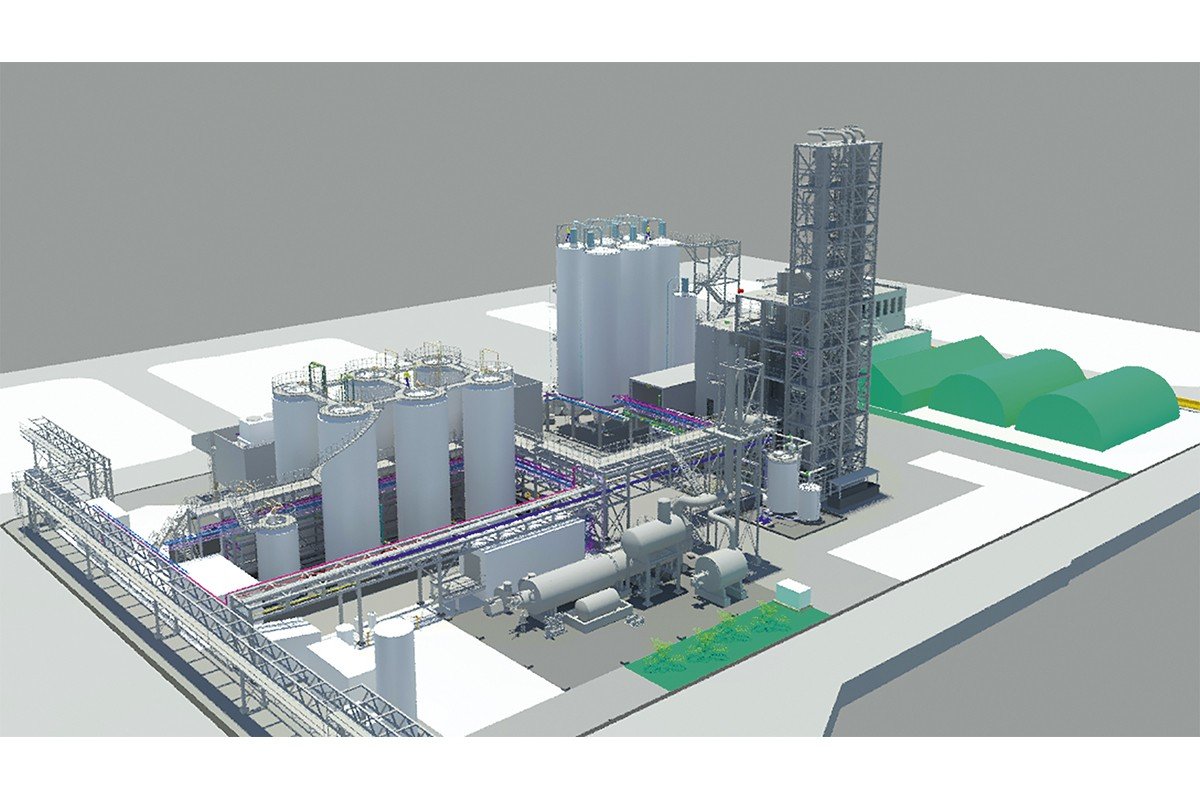
Synergies
L'usine de recyclage chimique se décline par toutes sortes de synergies sur le site d'Indaver. En effet, Indaver est autorisé à traiter les déchets sur le site, il y a un laboratoire, il y a de la vapeur et il y a de l'électricité. Deux éoliennes tournent sur le site (il y en aura d'autres) et des panneaux solaires seront installés. L'usine pilote requiert environ 2,5 MW d'électricité. Une première étude a été lancée en 2014. En 2017, elle menait à l'érection d'une installation pilote au LCT (Laboratory for Chemical Technology) de l'Université de Gand. Elle a été démantelée en novembre 2022 et reconstruite chez Indaver. « Tout tient dans deux conteneurs. »