ENGINEERINGNET.BE - Mais comment l’industrie de transformation pourrait-elle devenir neutre en carbone comme l’imposent les ambitions européennes ? S'agit-il d’une multitude de petits éléments contributifs ou l’industrie de transformation doit-elle embrasser des méthodes de production radicalement nouvelles ? Siemens s’est mis en quête de réponses adaptées à chaque entreprise.
Au cours de ces quinze dernières années, le rendement de l’industrie de transformation a doublé, mais les émissions de CO2 sont restées pratiquement au même niveau. Donc, prétendre que ces entreprises ne se seraient pas encore engagées sur la voie d'une durabilité accrue est un non-sens. Pourtant, considérée dans son entier, cette industrie représente encore 38% de la consommation mondiale d'énergie et 20% des émissions de CO2. Par conséquent, il y a encore pas mal de pain sur la planche.
« Mais en attendant, la cueillette des fruits à portée de main appartient déjà au passé », comme l’explique Kris Van Heurck, directeur des ventes Vertical Sales chez Siemens. « Comment allons-nous poursuivre l’optimisation des processus industriels dans les années à venir ? Telle est la question que se posent aujourd’hui bon nombre d’entreprises de l’industrie de transformation.
Une industrie qui, au demeurant, n’accueille pas en son sein que des entreprises (pétro)chimiques. Il y a lieu d’inclure également les secteurs qui suivent : alimentation et boissons, produits chimiques raffinés, gaz et pétrole. Autant de ramifications très différentes issues d’un même tronc, mais néanmoins confrontées aux mêmes enjeux : comment gagner en durabilité aujourd'hui ? Parce que le prix de revient du CO2 augmentera sensiblement dans les années à venir. L’Europe envisage également de procéder à une évaluation des émissions de CO2. »
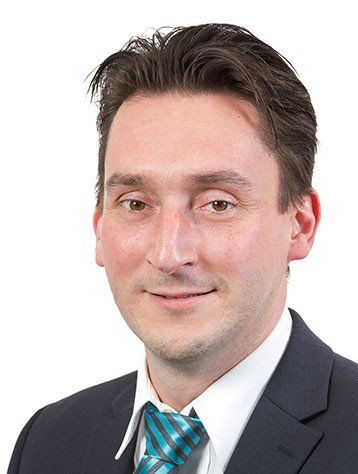
Énergie et matières premières
Il est temps de consentir à de nouveaux investissements. À cet égard, plus ils seront durables, plus les mécanismes de soutien pourront être sollicités à cette fin. Dans ce contexte, l’industrie de transformation n’échappera pas à l’électrification. Bon nombre d’entreprises se penchent déjà sur le remplacement d’équipements mus par des turbines à vapeur ou à gaz par des équipements à entraînement électrique.
« Mais l’électricité seule ne suffit certainement pas à résoudre tous les problèmes rencontrés. Il faudra recourir à un mix énergétique dans lequel l’hydrogène et d'autres hydrocarbures auront également un rôle à jouer », précise Van Heurck. « Toute source d’énergie verte présente des atouts et des inconvénients ; dès lors, il est capital d’y recourir au moment le plus opportun. De plus, il faut identifier toute source de chaleur résiduelle susceptible d’être utilisée ailleurs. » Une deuxième piste à étudier consiste à déterminer si l’alimentation des processus est susceptible d’être assurée au moyen de matières premières plus durables. « L’utilisation de matériaux recyclés est-elle envisageable ? À titre d’exemple, le caoutchouc tiré des pneus de voiture usagés permet de confectionner des éléments de construction durables pour l’industrie. »
Place aux données
Quelles que soient les voies qu’elles souhaitent emprunter, les entreprises de transformation devront avant tout chercher leur salut dans la technologie. « Des données, encore des données, toujours des données », prêche Van Heurck. « Tout d’abord pour faire le point sur la situation. Surveillance de la consommation d’énergie par exemple.
Afin d’apporter des améliorations à court et à long terme sur la base de données historiques et d’un suivi en temps réel. Les jumeaux numériques, en particulier, constituent une piste intéressante. La virtualisation partielle ou totale d’une unité de transformation et l’exécution d’un logiciel de simulation sur celle-ci permettent d’identifier les goulets d'étranglement et les optimisations envisageables sur les sites de production.
Nous comptons beaucoup sur la modélisation de processus pour déterminer l’influence de certains paramètres. Mais chez Siemens, le développement de modèles mis à disposition dans des bibliothèques permet de se livrer à des analyses comparatives. Par exemple, quel est le rendement de mon vapocraqueur par rapport à d’autres équipements ? »
Développement plus rapide et plus durable des vaccins
Une technologie qui repose également sur l’expérience pratique requise. Ainsi, la technique du jumeau numérique mise au point par Siemens a aidé GSK à développer plus rapidement certains vaccins. Au terme d’une démonstration de faisabilité concluante (Siemens et Atos) portant sur la production de particules d’un adjuvant de vaccin (substances renforçant l’immunogénicité d’antigènes), GSK s’est progressivement lancé dans la mise en œuvre de jumeaux numériques dans le cadre de ses activités de développement.
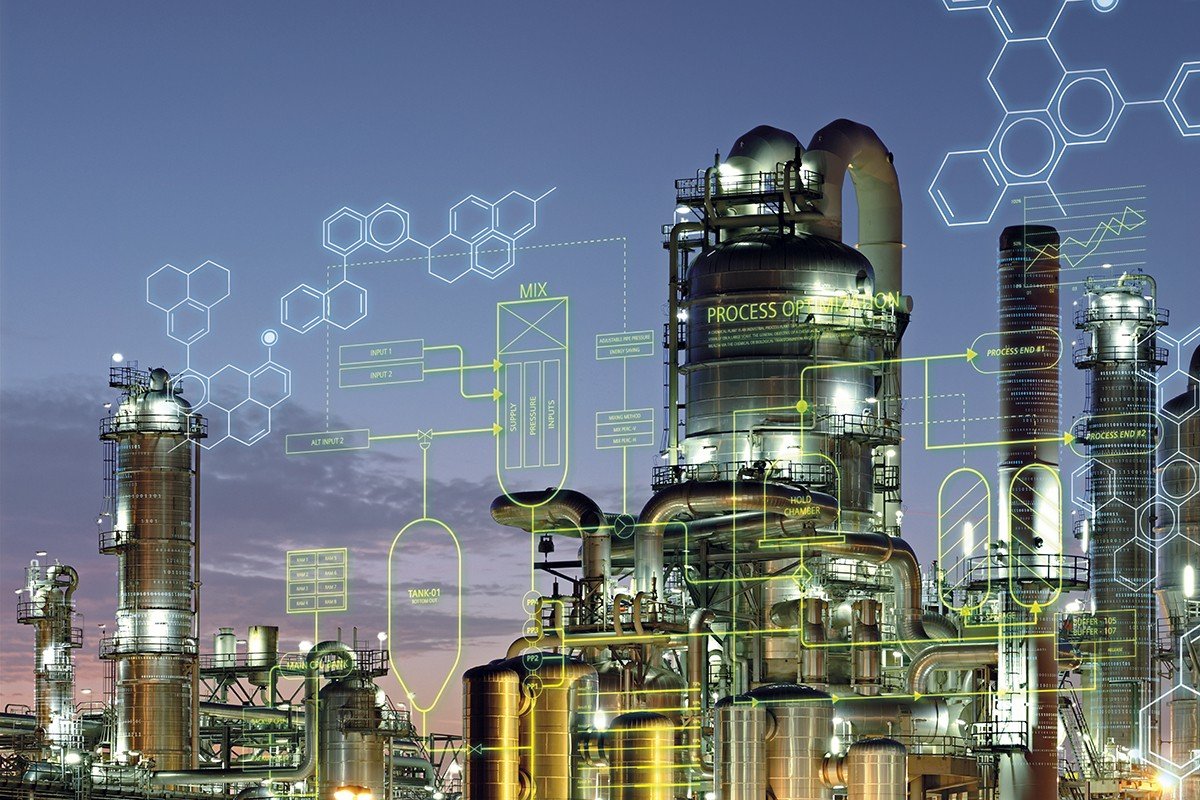
GSK s’est notamment penché sur les modalités d’utilisation de cette technique à un stade plus précoce d’un projet de vaccin. En effet, la conjugaison d’expériences et de modèles de jumeaux numériques livre rapidement les données indispensables pour confirmer telle ou telle théorie. À l’avenir, les jumeaux numériques permettront de réduire sensiblement le nombre des expériences réelles indispensables. Cette évolution contribuera à accroître la durabilité en raison de la baisse de la consommation d’énergie et de matériaux qui en résulte.
Réduction des émissions de CO2
Un deuxième exemple nous vient du Chemelot Campus, lequel se situe de l'autre côté de la frontière. Divers combustibles et gaz naturels produits sur le site assurent l’alimentation de cinq chaudières et d’une unité de cogénération affectée à la production de vapeur et d’électricité. Dans le but de réduire la consommation d’énergie et les émissions de CO2, SPSE a mis en oeuvre en 2016 l’outil d’optimisation énergétique gPROMS Utilities conçu par Siemens.
Cette solution se composait d’un Advisor (suivi et optimisation des activités en cours), d’un Planner (optimalisation de la gestion future du site) et d’un Engineer (bibliothèques de modèles évolués, conçus pour la gestion d’équipements d’utilité publique). L’optimisation des circuits de vapeur s’est traduite par une réduction des pertes de vapeur. Une sélection plus pointue du pilote s’est également traduite par une efficacité accrue. Bref, un investissement qui en valait largement la peine.
En effet, l’amortissement de cette solution n’aura pris que neuf mois à peine. De plus, son adoption s’est avérée payante pour l’environnement, comme en témoigne une réduction supplémentaire des émissions de CO2 de l’ordre de 3 à 7%. En outre, cette solution a permis d’identifier, au cours des trois premiers mois d’exploitation, un gisement d’économies supplémentaires de l’ordre de 2,4 à 5,6 millions d’euros par an.
Production de margarine à l’épreuve du temps
En tant que partenaire de choix, Siemens a déjà fait ses preuves dans le secteur de l'alimentation et des boissons. À titre d’exemple, l’entreprise a mis au point un nouveau système de contrôle des lots conçu pour piloter la production de margarine chez Vandemoortele. Principale exigence requise ? Intégration verticale.
En outre, une traçabilité bidirectionnelle automatique, un meilleur contrôle de la qualité en atelier, une appréhension en temps réel plus précise de la consommation de matières premières et une vue d’ensemble plus pertinente des différentes phases du processus considéré figuraient également dans le cahier des charges. Reposant concrètement sur le logiciel Simatic Batch et le système d’exploitation PCS 7, la solution standard fournie par Siemens se charge de la bonne exécution des étapes de la recette.
En sa qualité de Siemens Solution Partner, Actemium a assumé les responsabilités d’intégrateur pour ce qui concerne la programmation, la visualisation et une personnalisation adaptée à l'installation de Vandemoortele. Autant de solutions standard qui autorisent l’adoption du même système sans nécessiter une foule d’adaptations au sein des margarineries de Barcelone et de Dresde appartenant au même groupe.
Gamme étendue, vastes compétences
Fil conducteur ayant conduit le client à opter pour Siemens dans le cadre de ces projets ? « La numérisation est le point de départ de la durabilité ; cette observation s’applique à tous les secteurs d’activité. Après tout, la numérisation permet d’acquérir et de partager des connaissances. Mais ce n’est pas tout !
Siemens dispose de toutes les technologies, du plus petit capteur de mesure sur le terrain au logiciel le plus complexe pour obtenir des informations avec le concours de l’intelligence artificielle. Autant de données auxquelles s’ajoutent les connaissances acquises par notre personnel. Parce qu’il ne s’agit pas exclusivement de produits et de systèmes, mais aussi de l’élaboration de processus efficaces », conclut Van Heurck.
siemens.be/industrie
Montrer l’exemple
Dans le domaine du développement durable, Siemens fait oeuvre de pionnier depuis de nombreuses années et ne cesse de redoubler d’efforts. Parallèlement à la publication de son rapport de durabilité (ESG - gouvernance environnementale, sociétale et entrepreneuriale) couvrant l’exercice 2022, l’entreprise a annoncé de nouveaux objectifs encore plus ambitieux en matière de décarbonation ainsi que la réalisation d’investissements majeurs.
- Réduction de 46% des émissions de CO2 engendrées par les activités de l’entreprise depuis 2019
- Objectifs ambitieux : Réduction de 55% des émissions physiques de CO2 d’ici 2025 et de 90% d’ici 2030
- Prévention de l’émission de quelque 150 millions de tonnes de CO2 chez les clients grâce aux produits et solutions Siemens vendus au cours de l’exercice 2022
- Investissement de 650 millions d’euros affecté à la décarbonation des activités de l’entreprise d’ici 2030
- Investissement de 280 millions affecté à la formation essentielle et continue du personnel de l’entreprise au cours de l’exercice 2022