ENGINEERINGNET.BE - En effet, le SiC réagit de manière ‘indésirable’ à l’énergie ajoutée par le laser et il est difficile à usiner. Jusqu'à ce que Sebastian Meyers y consacre son doctorat et prouve avec une solution itérative que c'était possible.
Pendant ce temps, la recherche a évolué vers des géométries plus complexes et plus précises telles que les gyroïdes. Ces structures 3D autonomes forment un réseau hautement ordonné et connecté à très grande surface.
Des applications telles que les échangeurs de chaleur semblent prometteuses. Après quatre années supplémentaires de recherche fondamentale, Meyers, aujourd'hui chercheur postdoctoral à la KU Leuven et l'équipe AM se tournent vers les composants.
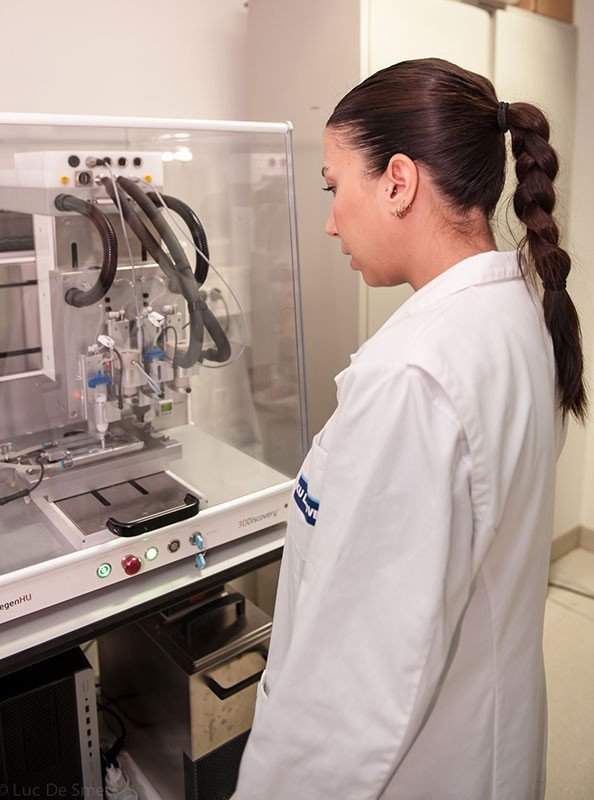
ESA
Un projet Early Technology Development au sein de la Open Space Innovation Platform de l'ESA s'est récemment terminé à l'université. Ce projet bilatéral de deux ans avait pour objectif de rendre mature la technologie SiC. Simultanément, les caractéristiques géométriques du matériau ont pu être explorées.
« Était étudié l'importance de l'influence de la rugosité de la surface et comment la réduire, non pas par le post-traitement mais par un réglage ‘in-process’. En fin de compte, il s'est avéré qu'il était nécessaire de planifier la rugosité restante pour obtenir des propriétés encore meilleures », déclarait Sebastian Meyers. En outre, une étude de cas sur le transfert de chaleur a comparé le SiC au cuivre et à l’aluminium. Le SiC était déjà plus performant que l’aluminium. Il est également 2,5 à 3 fois plus léger que le cuivre et sa température de fusion est bien plus élevée. Le cuivre fond à 1.083,4 °C et le SiC à 2.830 °C. Cette température de fusion élevée laisse présager des perspectives d’applications extrêmes.
Lors des voyages spatiaux, le SiC peut former un revêtement ou une couche barrière pour les missions dites de rentrée dans lesquelles des engins spatiaux ou des satellites pénètrent à grande vitesse dans l'atmosphère. Entre-temps, un deuxième projet de l'ESA est en cours depuis six mois dans le cadre duquel les chercheurs étudient ce que l'on appelle les ‘structures de morphing’ en céramique. « Nous combinons la couche de céramique avec un support métallique.
Les températures élevées déformeront le métal, mais le SiC lui-même a une très faible dilatation thermique. Cependant, un bouclier thermique SiC externe doit bouger avec la plaque métallique sous-jacente sans se briser. » Les éprouvettes que le groupe construira seront testées dans le plasmatron de l'Institut von Karman. « We make it and we break it. Pour apprendre », déclare Vleugels.
La résistance aux hautes températures, la très faible dilatation thermique, mais également sa résistance à la corrosion dans des environnements extrêmes promettent au SiC un avenir dans de nombreux milieux difficiles. Il pense à des revêtements capables de résister au sel fondu ou au plomb fondu. Mais il voit aussi d’autres opportunités, comme les pales de turbine dans les moteurs à réaction. « Imaginons des pales rotatives en céramique contenant des fibres de SiC. »
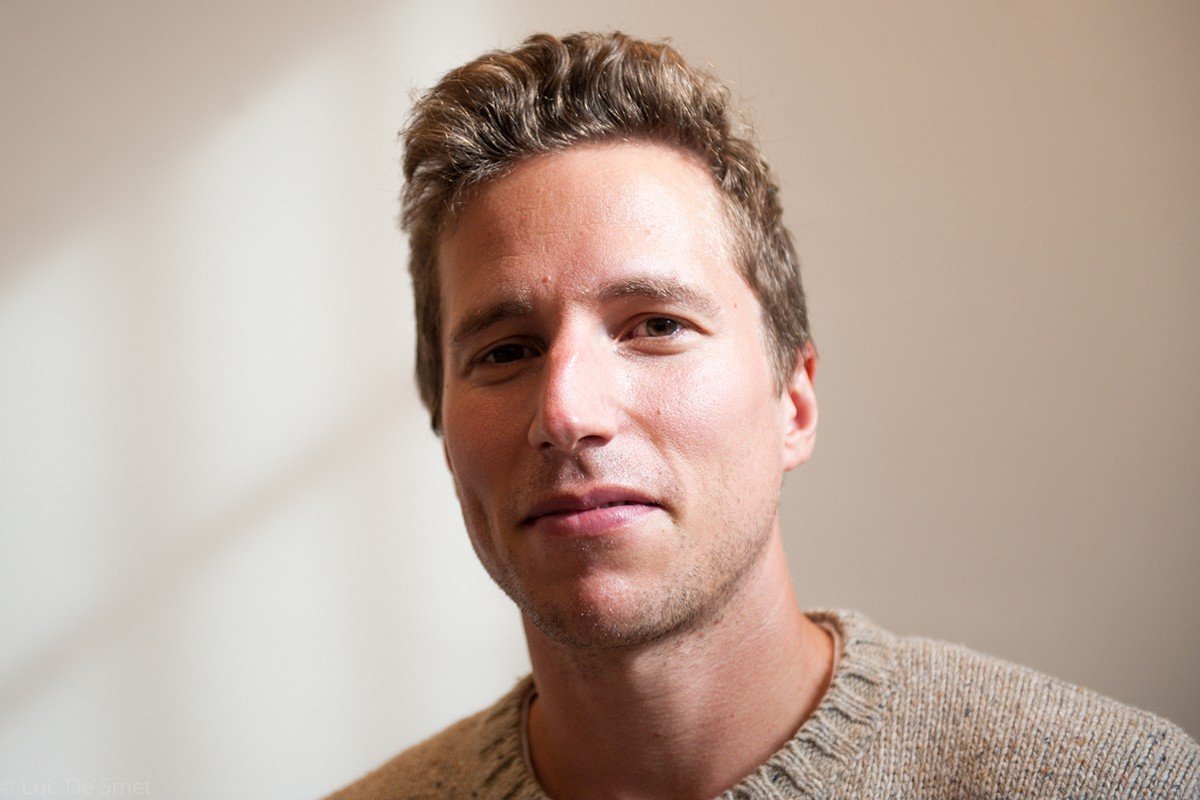
Process itératif
Lorsque Meyers a commencé son doctorat, personne ne pouvait imprimer du SiC. Si l'on chauffe le SiC jusqu'à sa température de fusion, il se décompose en Si et en C. « Nous avons mélangé du SiC avec du métal de Si que l'on peut faire fondre. Suit un process LPBF- on fusionne la poudre combinée dans un lit fluidisé à l'aide du laser - le silicium fond sous le laser et lie les particules de SiC entre elles », explique Meyers.
« Nous ajoutons ensuite du carbone à la pièce poreuse. Nous trempons la pièce imprimée dans une suspension en C. Ou bien nous travaillons avec un précurseur, une résine polymère pyrolysable, de telle manière que le carbone s'insère dans les pores. Nous infiltrons ensuite la pièce avec du silicium liquide à 1.500 °C. Le silicium remplit les pores et y réagit avec le carbone pour former du SiC supplémentaire. C'est du SiC formé par réaction. »
Cependant, ce process itératif plutôt complexe, permet d'obtenir des pièces de SiC imprimées au laser, sans retrait entre la conception et la pièce finale et sans pores, ce qui était auparavant impossible. Vleugels stipule que le process est tout à fait ‘durable’. Il s'alimente de ‘déchets’. « Nous extrayons le silicium de l’industrie des wafers. Des chutes. Le SiC est un déchet issu de la pyrolysation des pneus automobiles. »
La poudre de départ est par conséquent ‘super bon marché’. Actuellement quelques 25 kg pour 90 euros. Soit plus de dix fois moins cher que les poudres métalliques d'un LPBF. L'expédition est plus chère que le matériel lui-même.
Valeur ajoutée avec des multi-matériaux
Le parcours de recherche de Louvain parti de rien arrivait à quelque chose. Actuellement, la problématique devient plus complexe. « Au cours des cinq prochaines années, nous allons orienter notre développement vers l'amélioration de toutes sortes de propriétés et ... les multi-matériaux. Avec du titane par exemple. Mais plus on intègre de matériaux, plus les défis se multiplient … »
Vleugels souligne également une dialectique remarquable. « Maintenant que le process en production est presque sous contrôle, nous sommes confrontés aux limites actuelles de la technologie des imprimantes 3D, telles que la résolution et la vitesse d'impression. » Ce qui nécessite donc de nouveaux développements matériels et logiciels. L'accent est mis en premier lieu sur des applications telles que les échangeurs de chaleur.
« Finalement, les concepteurs qui modélisent ce genre d'échangeurs de chaleur depuis un certain temps pourront également passer à la pratique. » Des revêtements durables pour le monde nucléaire sont également envisagés. Mais « l'obtention des certificats exigés prendra beaucoup de temps »,
soupçonne Vleugels. Peut-être que les applications du SiC dans le monde médical prendront alors plus rapidement leur envol.
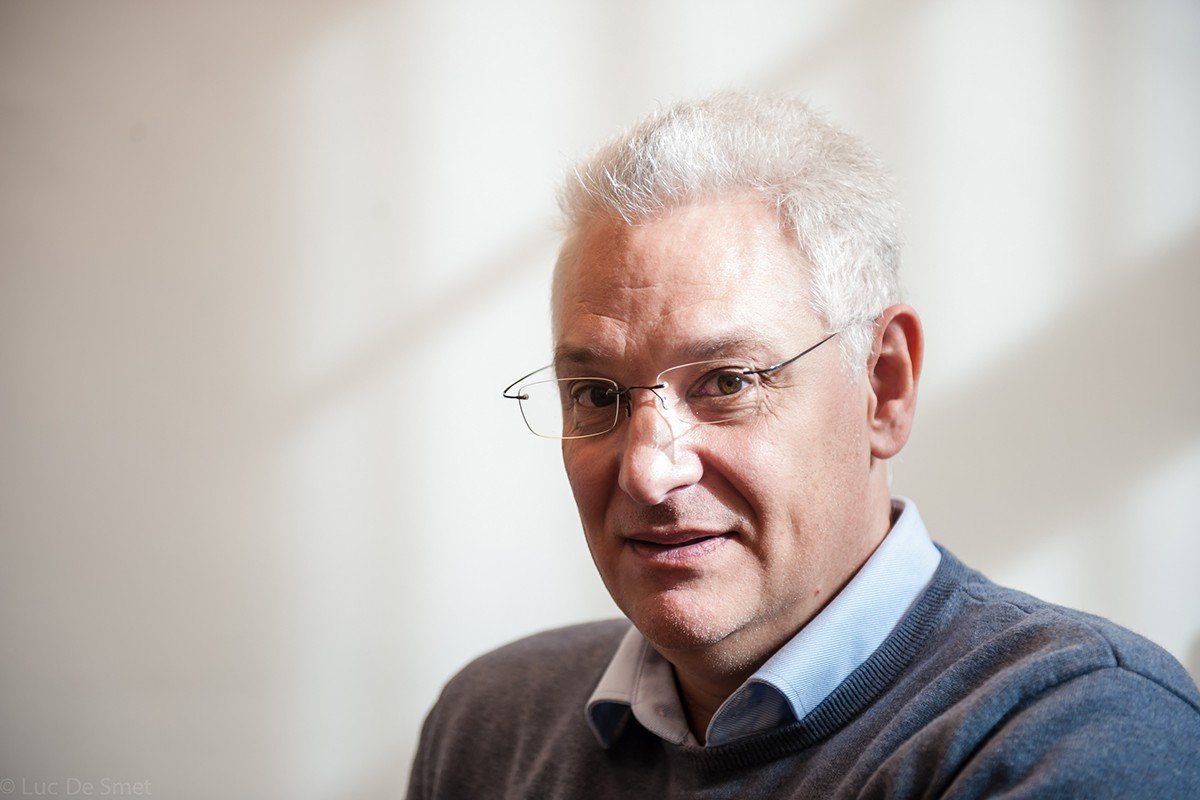
Le monde médical
Une fonctionnalité complètement différente pour les céramiques imprimées en 3D se découvre ici. L'irradiation FLASH (un puissant flash de protons sur la zone tumorale d'un seul coup) semble être plus efficace et physiquement moins nocif pour le corps du patient que d'irradier plusieurs fois avec un faisceau de protons de plus faible intensité. L'impact de l'irradiation FLASH full-body pourrait être considérablement réduit par l'usage de filtres imprimés en 3D adaptés à la taille du patient. Ces filtres, placés entre la source du faisceau et le patient, garantissent que le rayonnement ne cible que la zone nécessaire au traitement ; en outre ils contrôlent également la profondeur et la densité locale de l'irradiation.
Cela fait partie des recherches du Prof. Tom Depuydt à l'UZ de Louvain. Ion Beam Applications (IBA), d'Ottignies Louvain-la-Neuve, leader mondial des accélérateurs de particules pour la protonthérapie (traitement du cancer), serait semble-t-il impatient de voir ces développements. Vleugels souligne le mouvement pendulaire de la recherche sur l'impression 3D de céramiques techniques. « Nous avons d’abord étudié comment imprimer du dioxyde de zirconium (ZrO2) de manière très dense. Maintenant, nous étudions comment fabriquer un tel implant non seulement dur, chimiquement inerte et biocompatible, mais également poreux et pouvant servir de plateforme de base pour les médicaments. »
Dans le monde dentaire, l'on envisage des couronnes dentaires imprimées en 3D qui libèrent des produits pharmaceutiques ou des médicaments de manière contrôlée. « Le projet de recherche européen NOMAD débutait à ce sujet en décembre 2022, coordonné par la collègue la Prof. Annabel Braem. » D'autres chercheurs visent une telle libération contrôlée du médicament via la vis d'un implant dentaire pour favoriser l'ostéo-intégration et éviter ou éliminer les infections bactériennes ... « Dans les deux cas, le lien avec la microbiologie est clair », explique Arnout Dejans, coordonnateur à l'Institut AM de la KU Leuven.
L’Additive Manufacturing Institute a été fondé à la KU Leuven en 2022. L'intention de cette plateforme faîtière est de réaliser une collaboration interdisciplinaire entre différents départements, en l'occurrence ici la KU Leuven et l'UZ Leuven. L'activité cible la production d'objets à partir de données de modèles 3D, le développement de matériaux et de matières premières (feedstock), le développement de process ou de besoins spécifiques pour des applications où l’impression en 3D peut créer de la valeur ajoutée.
L'AM Institute compte quelques 200 membres, dont environ 50 professeurs qui travaillent dans des domaines liés à la fabrication additive ; l'accent cependant est mis sur les départements de génie mécanique et de science des matériaux. La coordination est faite par Arnout Dejans. « L’objectif est de disposer d'un institut autonome. Cela nécessite un business plan, de la recherche scientifique, de l'enseignement, des services et des conseils, de la recherche de preuve de concept, de la mise à l'échelle ... L'initiateur et le directeur est le professeur Brecht Van Hooreweder, des process et systèmes de fabrication (MaPS) au département de génie mécanique.