ENGINEERINGNET.BE Pour l’atténuer autant que possible, les essuie-glaces des véhicules électriques sont fabriqués dans un ‘caoutchouc silencieux’. C’est ce que nous avons appris lors de la visite de l’usine et du centre de compétences en caoutchouc et essuie-glaces de Bosch à Tirlemont, en activité depuis 1974.
En 2023, Bosch a investi 11 millions d’euros dans une ligne d’extrusion de caoutchouc pour les balais d’essuie-glaces. La ligne a été testée en vue d’un démarrage à la mi-octobre. En 2025, elle assurera la moitié de la production. Elle est ergonomiquement moins contraignante pour les opérateurs, consomme moitié moins d’énergie que la précédente et 90% de sel en moins.
Le sel ajouté dans un bain d’eau chaude sert au transfert thermique lors de la vulcanisation du caoutchouc. Jadis, les spoilers en plastique étaient achetés. Depuis cette année, deux lignes d’extrusion de plastique en produisent. L’année prochaine, l’emballage des kits simples et doubles des balais essuie-glaces sera automatisé.
Excellence
« Que notre centre de compétence soit situé en Belgique n’a rien de surprenant », lance le plant manager Werner Richter (50), qui veut souligner le savoir-faire acquis et entretenu depuis des décennies sur le site. « Ce niveau d’excellence demande des efforts soutenus durant plusieurs générations. Depuis 1974, les chercheurs de Bosch à Tirlemont ont déposé plus de 3.000 brevets. »
« Notre groupe R&D compte 101 développeurs dont 53 en Belgique. Nous avons des collaborateurs au Mexique, en Serbie et dans deux sites en Chine », poursuit Dirk Herinckx, R&D manager. Le centre de compétence se focalise sur les connaissances technologiques et les processus. Au niveau mondial, environ 20% des balais d’essuie-glaces Bosch et 70% du ‘caoutchouc’ viennent de Tirlemont.
L’accent est mis sur le marché de remplacement et la gamme d’essuyage. Le marché après-vente est donc un multiple de l’équipement original. Aujourd’hui, l’usine produit notamment la troisième génération Aerotwin selon une nouvelle formulation de caoutchouc (polymère EPDM) et un revêtement Power Protection Plus. Une prouesse technologique.
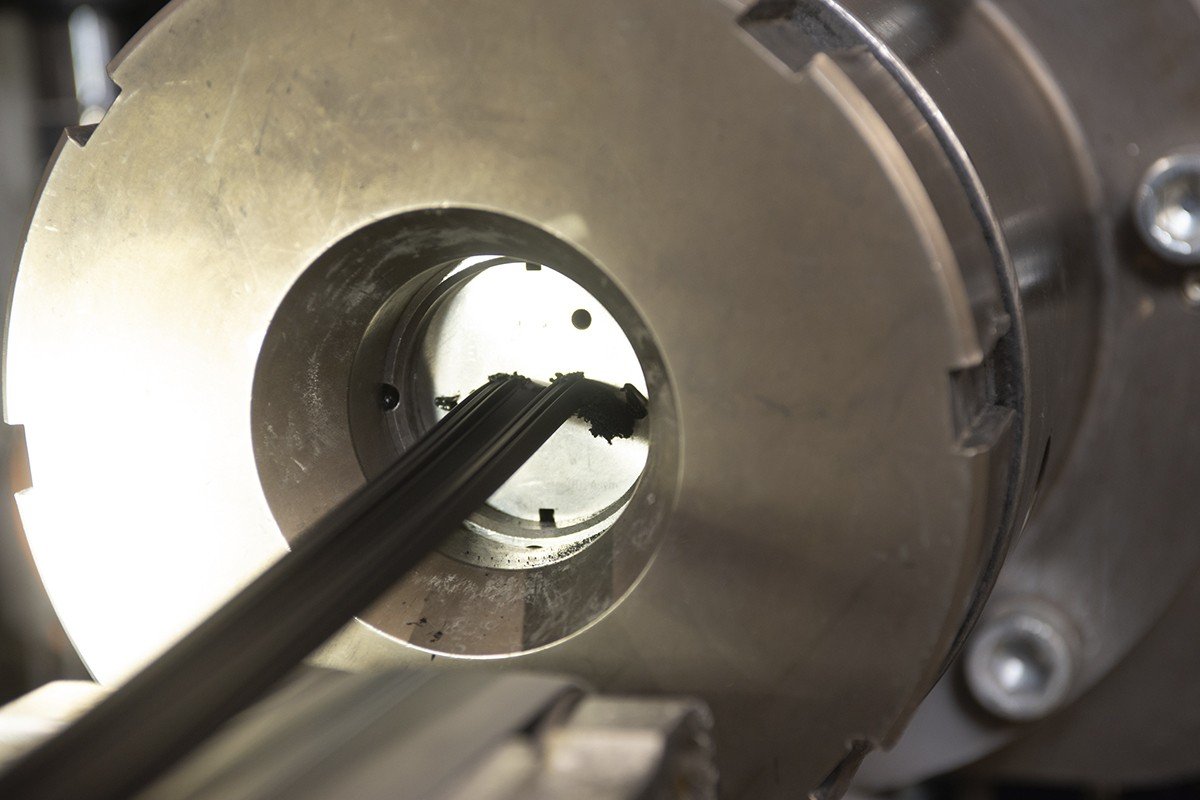
Ressort à lames et gomme d’essuyage
Les balais d’essuie-glaces ont évolué d’une forme rigide vers une forme conventionnelle qui absorbe les forces au centre du balai et les répartit sur l’ensemble du balai. En 2020, un modèle ultra plat est lancé qui répartit la pression uniformément sur le pare-brise, sans support de cadre. Aujourd’hui, un spoiler maintient l’essuie-glace contre le pare-brise lors de vitesses élevées, sans bruit de vent. L’adaptateur qui connecte le balai à l’essuie-glace de la voiture y contribue également.
« Nous produisons 100.000 balais d’essuie-glaces Aerotwin par jour », déclare Mike De Cuypere, responsable de la production au sein du groupe. Un ressort à double lame adapte le balai à la courbure du pare-brise. Des rouleaux de cintrage servocommandés plient l’acier du ressort avec du chrome en fonction du véhicule. Chaque millimètre a un rayon bien défini. Une couche PET sur les ressorts permet ultérieurement de souder par ultrasons les extrémités en plastique et l’adaptateur central. La gomme d’essuyage ne contient plus de caoutchouc mais est un mélange de matériaux synthétiques : de l’EPDM résistant à la chaleur, du noir de carbone, …
Le profil (d’extrémité) de la gomme d’essuyage est crucial car il garantit un travail uniforme et efficace dans les deux sens – vers le haut et le bas – par la lèvre d’essuyage. Le côté d’essuyage de la lèvre doit être parfaitement lisse. Toute erreur supérieure à 30 microns entraîne des traces sur le pare-brise. La gomme d’essuyage n’est plus recouverte de graphite mais d’une poudre de polyéthylène UHW (à haut poids moléculaire) ultra-fine de de 10 microns qui est pulvérisée au pistolet électrostatique. Une station plasma fait fondre la ‘monocouche’ sur le plastique. La gomme d’essuyage est ensuite découpée sur mesure. Sur la ligne de montage, elle est insérée dans les ressorts métalliques, le spoiler en plastique et les embouts sont fixés et un laser grave la marque et autres données sur le plastique.
Nous sommes passés devant les chambres climatiques, mais nous avons pu voir une configuration dotée d’une caméra rapide qui enregistre les forces et la déformation des balais sur le pare-brise, ce qui fournit de l’information pour les développements ultérieurs. Ailleurs, des caméras visualisent la qualité d’essuyage d’échantillons. « Aujourd’hui nous travaillons à partir des observations des opérateurs, mais nous construisons actuellement un système IA pour obtenir des évaluations plus objectives », explique Bart Robijns, Program Manager Bosch Wiper Development.
Bosch conditionne généralement les kits d’essuie-glaces des côtés conducteur et passager dans un seul emballage. La machine de conditionnement travaille par lots (à longueur). Le remplacement du plateau protecteur en plastique PET – qui accueille les balais d’essuie-glaces - par un matériau à base de fibres de cellulose permet d’économiser plus de 350 tonnes de plastique par an. Une deuxième machine d’emballage, qui sera mise en service l’année prochaine, permettra d’emballer des balais individuels.
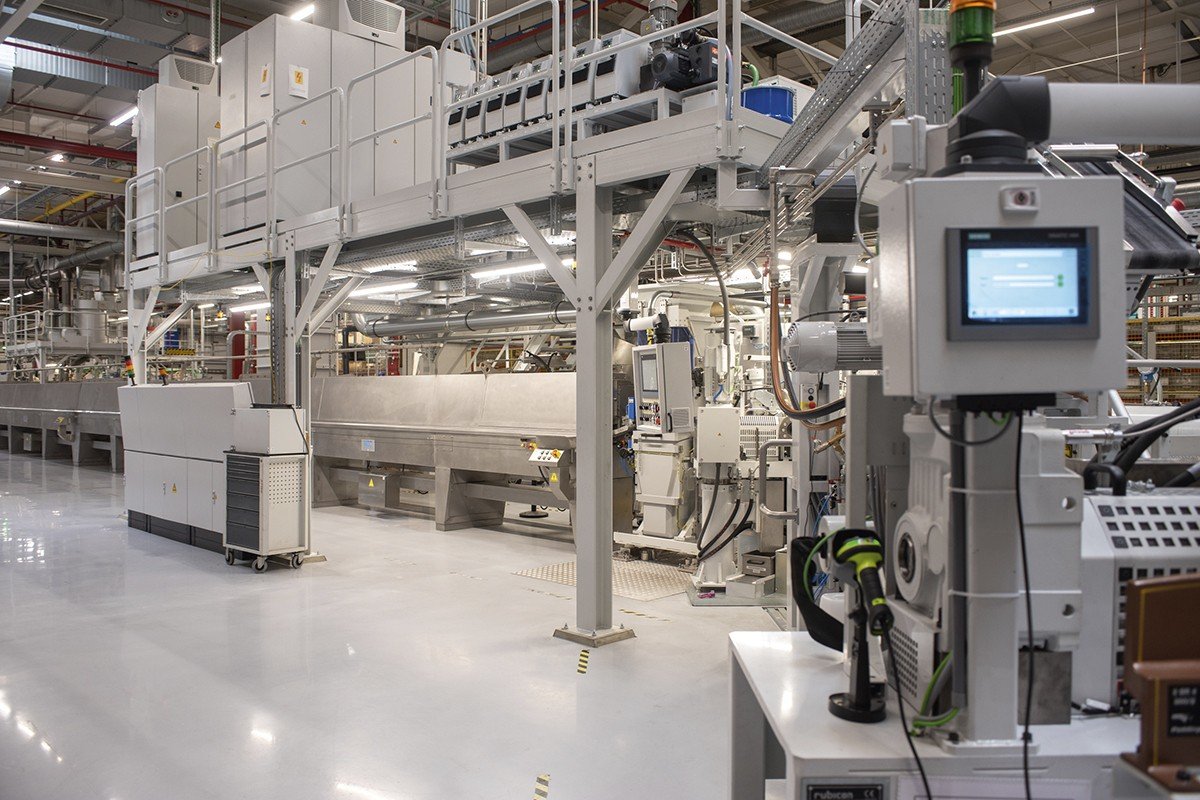
Caoutchouc
L’ancienne production en lots du ‘caoutchouc’ est presque entièrement absorbée dans une production en flux ou en continu. Les PLC surveillent le dosage des 10 à 14 matières premières. Le TPV (vulcanisat thermoplastique) obtenu se compose d’un caoutchouc EPDM vulcanisé dans une matrice PP. Après le laminage, la masse homogène est poussée à travers des filtres métalliques à plus de 200 bars pour retenir les dernières impuretés. La bande passe par un vide qui aspire la dernière humidité avant d’être pressée dans une ligne de calibrage.
« Deux machines d’électroérosion à fil dans l’atelier peuvent fournir un nouveau produit en 24 heures », explique Philippe Collin, Group Leader Wiper Rubber Production. L’outil final délivre un brin sans fin de deux gommes d’essuyage reliées entre elles par le côté d’essuyage fin. Il passe par un bain d’eau salée à 200°C pour obtenir l’élasticité. Vient ensuite le refroidissement et le rinçage à l’eau. Un ‘couteau à pizza’ coupe la double gomme d’essuyage en deux. « La technique de coupe en ligne a été développée ici », ajoute Gert Vanderheyden, Director Mini Factory Rubber. Elle permet d’obtenir une solution en une passe et d’économiser du matériau. Le couteau coupe 20 km de produit avant d’être changé.
Les trois lignes d’extrusion fonctionnent en continu. La ligne la plus récente produit autant que les deux autres réunies. Elle est adaptable selon le type de production et les traitements souhaités. Bosch adapte ses balais aux pare-brises. Les constructeurs asiatiques sont plus enclins à opter pour un traitement hydrophobe du pare-brise, tandis que les constructeurs européens préfèrent une solution hydrophile et des essuie-glaces plus silencieux. La course vers une solution capable de desservir les deux marchés est donc ouverte. En attendant, les gommes d’essuyage des clients ayant des exigences sonores plus élevées reçoivent un second revêtement et un traitement plasma. Le tout sur le même ligne.