ENGINEERINGNET.BE - SiC reageert immers ‘ongewenst’ op de energie die de laser toevoegt en is moeilijk bewerkbaar. Tot Sebastian Meyers er zijn doctoraat aan wijdde en met een meerstappenoplossing bewees dat het wél kon.
Ondertussen evolueerde het onderzoek naar meer complexe en accurate geometrieën zoals gyroïdes. Deze vrijstaande 3D-structuren vormen een zeer geordend en aaneengesloten netwerk met een zeer groot oppervlak. Toepassingen als warmtewisselaars lijken veelbelovend. Na nog eens vier jaar basisonderzoek, kijken Meyers, nu Postdoctoral Researcher bij KU Leuven, en het AM-team richting componenten.
ESA
Onlangs liep aan de universiteit een Early Technology Development project binnen het Open Space Innovation Platform van ESA af. Dit tweejarig bilateraal project moest de SiC technologie matuurder maken. Tegelijk konden onder meer de geometrische mogelijkheden van het materiaal verkend worden. “Er is onderzocht hoe groot de invloed van oppervlakteruwheid is en hoe we die kunnen verminderen, niet door nabewerken maar door in-process tuning. Uiteindelijk bleek dat nabewerken van de resterende ruwheid toch noodzakelijk was om nóg betere eigenschappen te bekomen”, gaf Sebastian Meyers mee.
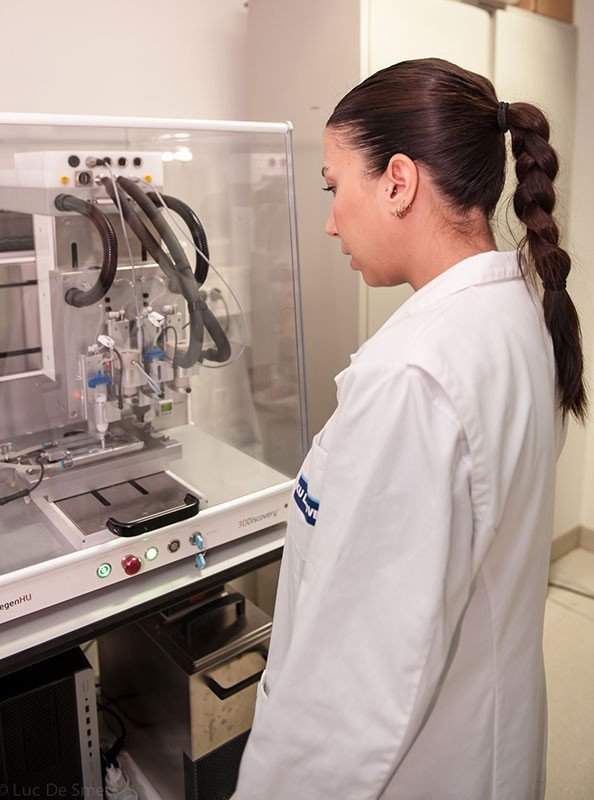
Voorts vergeleek een warmteoverdracht casestudie SiC met koper en aluminium. SiC presteerde alvast beter dan aluminium. SiC is bovendien 2,5 à 3 keer lichter dan koper en zijn smelttemperatuur is veel hoger. Koper smelt bij 1.083,4 °C en SiC bij 2.830 °C. Die hoge smelttemperatuur wijst naar mogelijkheden voor extreme toepassingen. In de ruimtevaart kan SiC wellicht een barrièrecoating of -laag vormen voor zogenaamde re-entry missies waarbij ruimtetoestellen of satellieten tegen hoge snelheid de atmosfeer induiken. Ondertussen loopt er al zes maanden een tweede ESA-project waarbij de onderzoekers kijken naar zogenaamde ‘morphing structuren’ uit keramiek.
“We combineren de keramieklaag met een metalen drager. Hoge temperaturen zullen het metaal vervormen maar SiC kent zelf een zeer lage thermische uitzetting. Een extern SiC hitteschild moet echter meebewegen met de onderliggende metalen plaat zonder te breken.” De proefstukken, die de groep zal bouwen, zullen bij het von Karman instituut in de plasmatron worden getest. “We make it and we break it. Om te leren”, zegt Vleugels.
De hoge temperatuurvastheid, de zeer lage thermische uitzetting maar ook zijn corrosiebestendigheid in extreme omgevingen beloven SiC een toekomst in heel wat uitdagende omgevingen. Hij denkt aan coatings die stand houden tegen gesmolten zout of gesmolten lood. Maar hij ziet ook andere mogelijkheden, als turbinebladen in straalmotoren. “Denk aan roterende keramische bladen met daarin vezels van SiC.”
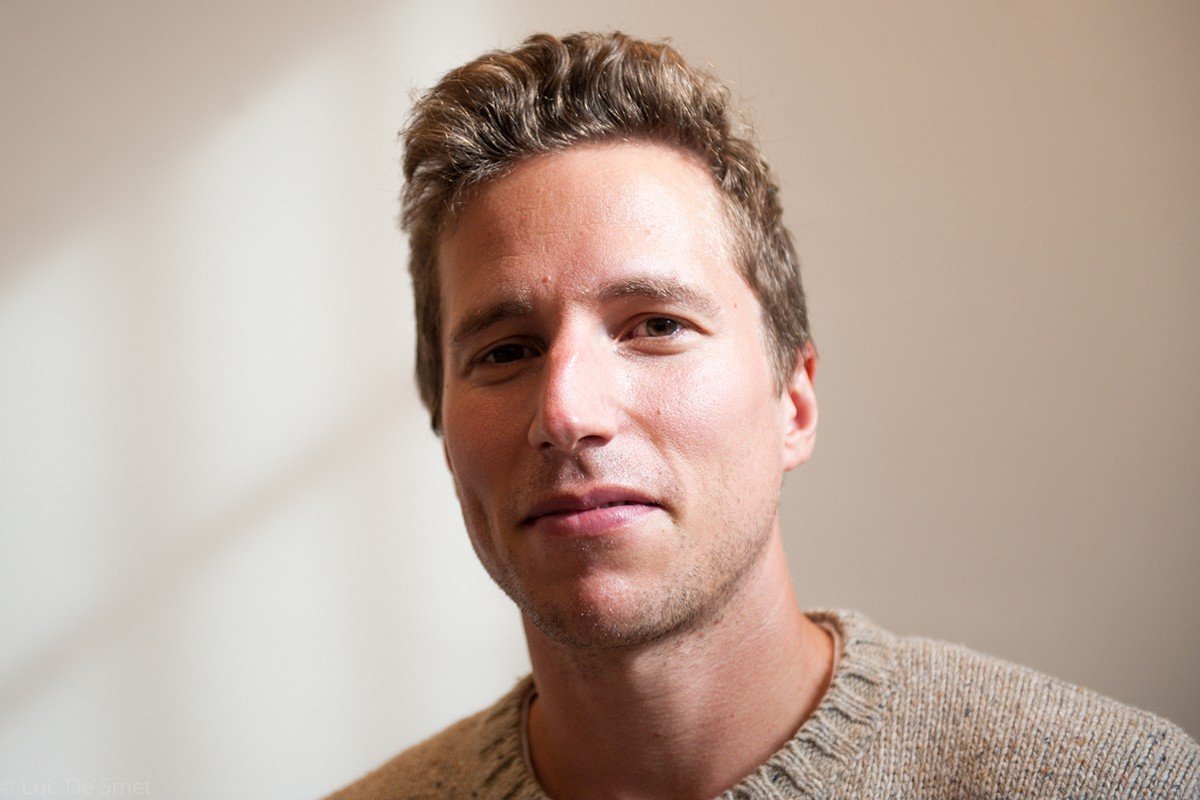
Meerstappenproces
Toen Meyers aan zijn doctoraat begon, kon niemand SiC printen. Als je SiC opwarmt tot zijn smelttemperatuur, valt het uiteen in Si en C. “Wij mengden SiC met Si metaal, dat je wel kunt smelten. Als je dat LPBF’t -als je dus het gecombineerde poeder in een poederbed met de laser fuseert- dan smelt het silicium onder de laser en dat bindt de SiC deeltjes aan elkaar”, legt Meyers uit. “Aan het poreuze stuk voegen we vervolgens koolstof toe. We dippen het geprinte stuk in een C-suspensie. Of we werken met een precursor, een polymeerhars dat je kan pyroliseren, zodat er koolstof achterblijft in de gaatjes. Vervolgens infiltreren we het stuk met vloeibaar silicium bij 1.500 °C.
Het silicium vult de poriën op en reageert met de koolstof tot extra SiC. Reactiegevormd SiC.” Het eerder moeizame meerstappenproces resulteert echter wel in lasergeprinte stukken SiC, zonder krimp tussen ontwerp en het finale stuk en zonder poriën, wat voorheen onmogelijk was. Vleugels merkt op dat het proces vrij ‘duurzaam’ is. Het voedt zich met ‘afvalmaterialen’. “De silicium halen we uit de waferindustrie. Snijafval. Het SiC is een afvalproduct van het pyroliseren van autobanden.” Het startpoeder is dan ook ‘supergoedkoop’. Vandaag zo’n 25 kg voor 90 euro. Of meer dan tien keer goedkoper dan metaalpoeders voor LPBF. De verzending is duurder dan het materiaal zelf.
Toegevoegde waarde met multi-materialen
Het Leuvense onderzoekspad leidde van niets naar iets. Nu voert het naar iets complexer. “De volgende vijf jaar schuiven we met de ontwikkeling naar het verbeteren van allerlei eigenschappen en … multimaterialen. Met titanium, bijvoorbeeld. Maar hoe meer materialen je integreert, des te meer uitdagingen …” Tevens wijst Vleugels op een opmerkelijke dialectiek.
“Nu de productieroute zowat onder controle is, stoten we op de huidige beperkingen van de 3D-printertechnologie zoals resolutie en printsnelheid.” Wat dus nieuwe hard- en softwareontwikkelingen vergt. Eerst en vooral wordt gewed op functies als warmtewisselaar. “Eindelijk zullen ontwerpers die al langer dergelijke warmtewisselaars modelleerden ze ook in de praktijk kunnen realiseren.” Er wordt ook gedacht aan duurzame coatings voor de nucleaire wereld maar “het bekomen van de nodige certificaten zal wel een hele tijd vergen”, vermoedt Vleugels. Misschien lopen SiC toepassingen in de medische wereld dan sneller van start.
Medische wereld
Daar blijkt een heel andere functionaliteit voor 3D-geprinte keramiek. FLASH bestraling (een ‘alles in één keer’ krachtige protonenflits op de tumorzone) lijkt vooralsnog efficiënter en fysiek minder schadelijk voor het lichaam van de patiënt dan het meermaals bestralen met een zwakkere protonenbundel.
Men zou de impact van full-body FLASH bestralingen fors kunnen verminderen door gebruik te maken van 3D-geprinte filters op de maat van de patiënt. Deze filters, die tussen de straalbron en de patiënt komen, zorgen ervoor dat de bestraling alleen daar komt waar die nodig is voor de behandeling, maar ze sturen bovendien ook de diepte en de lokale densiteit van de bestraling. Dit is deel van onderzoek door prof. Tom Depuydt aan UZ Leuven.
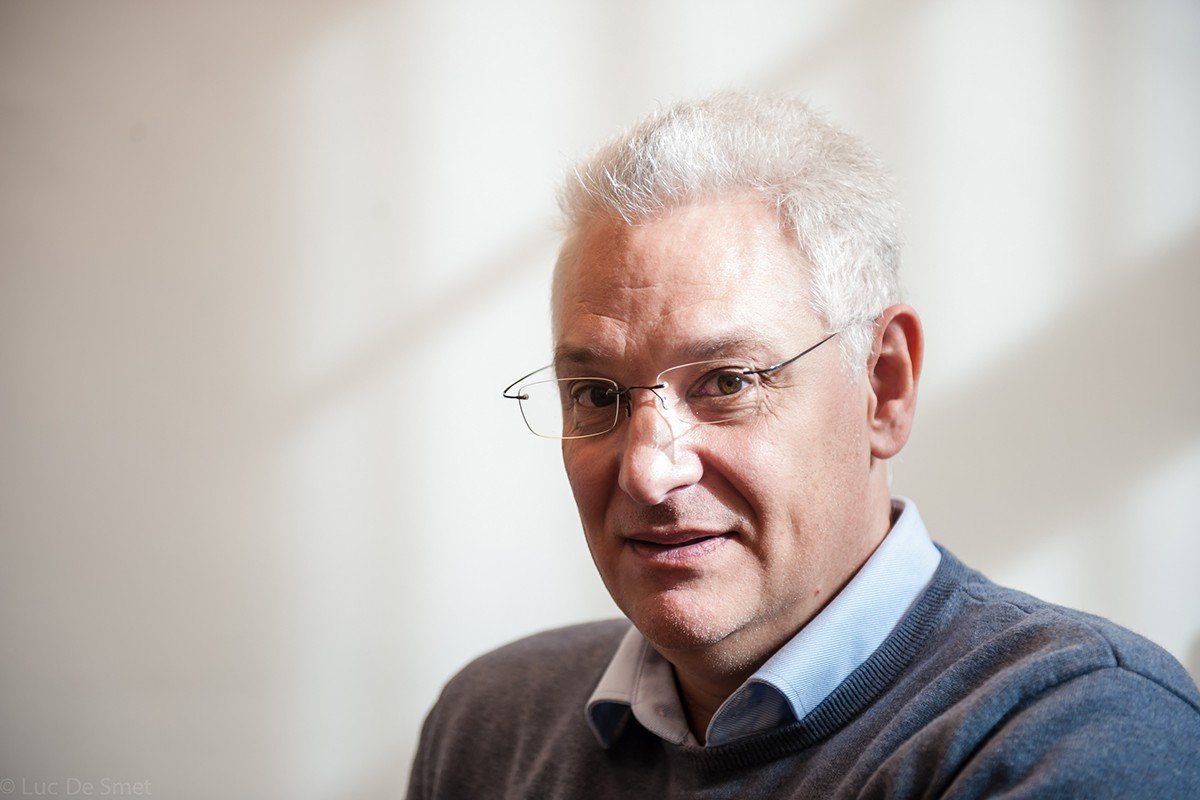
Naar verluidt kijkt Ion Beam Applications (IBA), uit Ottignies Louvain-la-Neuve, een wereldleider in deeltjesversnellers voor protontherapie (voor kankerbehandelingen) uit naar de ontwikkelingen. Vleugels wijst op de pendelbeweging van het onderzoek naar het 3D-printen van technische keramieken.
“Eerst onderzochten we hoe we zirconium dioxide (ZrO2) heel dens konden printen. Nu onderzoeken we hoe we zo’n implantaat niet alleen hard, chemisch inert en biocompatibel kunnen maken maar ook nog poreus en draagplatform voor medicijnen.” In de dentale wereld wordt gedacht aan 3D-geprinte tandkroontjes die op een gecontroleerde manier farmaceutische producten of geneesmiddelen vrijgeven. “Hierrond startte in december 2022 het Europees onderzoeksproject NOMAD, dat collega prof. Annabel Braem coördineert.”
Andere onderzoekers mikken op zo’n controlled drug release via de schroef van een tandimplantaat om osseo-integratie te bevorderen en bacteriële infecties te vermijden of te elimineren … “In beide gevallen is de link met microbiologie duidelijk”, zegt Arnout Dejans, die het KU Leuven AM Instituut coördineert.
Additive Manufacturing Instituut
In 2022 is aan de KU Leuven het Additive Manufacturing Instituut opgericht. De bedoeling van dit overkoepelend platform is een interdisciplinaire samenwerking te realiseren tussen verschillende departementen, in dit geval van de KU Leuven en het UZ Leuven, rond het produceren van voorwerpen uit 3D-modelgegevens, materiaal- en feedstockontwikkeling, procesontwikkeling of toepassingsspecifieke noden waarbij 3D-printen toegevoegde waarde kan creëren.
Het AM-Instituut telt ongeveer 200 leden waarvan een 50-tal proffen die iets rond AM doen maar de focus ligt wel bij de departementen Werktuigkunde en Materiaalkunde. Arnout Dejans coördineert. “Een zelfbedruipend instituut is het opzet. Dat vergt een businessplan, wetenschappelijk onderzoek, educatie, service & consulting, proof of concept onderzoek, upscaling …” Initiatiefnemer en directeur is prof Brecht Van Hooreweder, Maakprocessen en -Systemen (MaPS) aan het Departement Werktuigkunde.