ENGINEERINGNET.BE - Maar hoe kan de procesindustrie koolstofneutraal worden zoals de Europese ambities voorschrijven? Is het een kwestie van vele kleine beetjes die zullen helpen of moet de procesindustrie radicaal nieuwe productiemethodes omarmen? Siemens gaat voor elk bedrijf mee op zoek naar het juiste antwoord.
De voorbije vijftien jaar verdubbelde de doorloop binnen de procesindustrie, maar bleven de CO2-emissies nagenoeg op hetzelfde niveau. Zeggen dat deze bedrijven de weg naar meer duurzaamheid nog niet zijn ingeslagen is dus onzin. Toch is de industrie op zijn geheel wel nog verantwoordelijk voor 38% van het globale energieverbruik en 20% van de CO2-emissies. Er blijft dus werk aan de winkel. “Maar het laaghangend fruit is intussen geplukt”, opent Kris Van Heurck, sales manager Vertical Sales bij Siemens.
“Hoe gaan we de komende jaren de processen nu verder optimaliseren? Dat is de vraag waar veel bedrijven in de procesindustrie vandaag mee worstelen. Een industrie die overigens meer omvat dan alleen maar (petro)chemische bedrijven. Wij rekenen er ook food & beverage, fine chemicals en gas & oil onder. Heel verschillende takken van sport, maar wel met dezelfde topics die spelen: hoe nu verder verduurzamen? Want de kostprijs van CO2 zal de komende jaren flink stijgen. Europa denkt eveneens aan CO2-taxatie.”
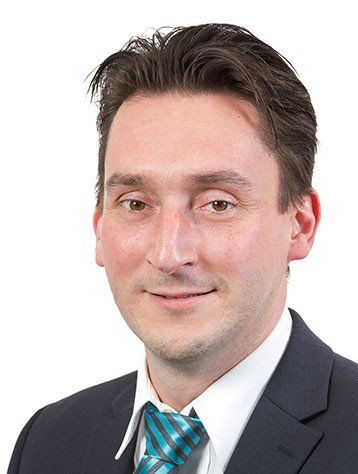
Kijken naar energie en naar feedstock
Tijd voor verdere investeringen dus en hoe duurzamer die zijn, hoe meer steunmechanismes hiervoor aangesproken kunnen worden. Aan elektrificatie zal de procesindustrie niet ontsnappen in dit verhaal. Veel bedrijven onderzoeken al of ze processen op basis van stoom- of gasturbines kunnen inruilen voor elektrisch aangedreven exemplaren.
“Maar met elektriciteit alleen, kan zeker niet alles opgelost worden. Het zal een mix worden waarin ook waterstof en andere koolwaterstoffen een rol te vervullen hebben”, weet Van Heurck. “Elke groene energiebron heeft zijn sterktes en zwaktes, het is zaak ze daarom op het beste moment toe te passen. En bovendien te zien of er ook geen restwarmte in de eigen processen aanwezig is die elders van toepassing kan zijn.” Een tweede piste die onderzocht wordt is of de processen gevoed kunnen worden met een duurzamere feedstock. “Kan er recyclaat worden toegepast? Het rubber van autobanden is bijvoorbeeld een mogelijkheid om tot duurzame bouwstenen voor de industrie te komen.”
Vooruit met data
Welke pistes ze ook willen behandelen, procesbedrijven zullen in de eerste plaats hun heil moeten zoeken in technologie. “Data, data, data”, predikt Van Heurck. “Eerst om in kaart te brengen wat de situatie is. Energiemonitoring bijvoorbeeld. Om dan op basis van historische data en real-time monitoring verbeteringen op korte en lange termijn te realiseren. Vooral digital twins werpen zich op als een interessante piste.
Door een procesinstallatie, deels of volledig, te virtualiseren en er simulatie-software op los te laten, kan je binnen de eigen productiesites bottlenecks en mogelijke optimaliseringen identificeren. We verwachten veel van proces modelling om de invloed van bepaalde parameters te achterhalen. Maar we hebben bij Siemens ook modellen ontwikkeld die beschikbaar zijn in bibliotheken waarmee je kan benchmarken. Hoe efficiënt presteert mijn steamcracker bijvoorbeeld ten opzichte van andere?”
Sneller en duurzamer vaccins ontwikkelen
Technologie die ook met de nodige praktijkervaring ondersteund wordt. Zo hielp de digital twin technologie van Siemens GSK om sneller vaccins te ontwikkelen. Na een geslaagde proof of concept met Siemens en Atos die focuste op de productie van partikels van een vaccin adjuvant (stoffen die de immunogeniciteit van antigenen versterken), is GSK geleidelijk begonnen met de implementatie van digital twins in zijn ontwikkelingsactiviteiten.
Het onderzoekt onder andere hoe deze technologie in een vroeger stadium van een vaccinproject nuttig kan zijn. De combinatie van experimenten en de digital twin modellen levert immers snel de gegevens op die nodig zijn om theorieën te bevestigen. In de toekomst zouden er dankzij digital twins drastisch minder echte experimenten nodig zijn, wat op zijn beurt helpt om de duurzaamheid te verhogen, omdat er minder materialen en energie worden verbruikt.
CO2-emissies doen dalen
Een tweede voorbeeld komt van vlak over de grens op de Chemelot Campus. Er worden natuurlijke gassen en brandstoffen geproduceerd op de site en verdeeld over vijf boilers en een WKK-unit om stoom en elektriciteit te produceren. Om het energieverbruik en de CO2-emissies te doen dalen implementeerde SPSE in 2016 de gPROMS Utilities tool voor energieoptimalisatie van Siemens. Een oplossing die bestond uit een Advisor (monitoring en optimaliseren huidige activiteiten), Planner (optimaliseren van het toekomstige sitebeheer) en Engineer (geavanceerde modelbibliotheken om nutsvoorzieningen te beheren).
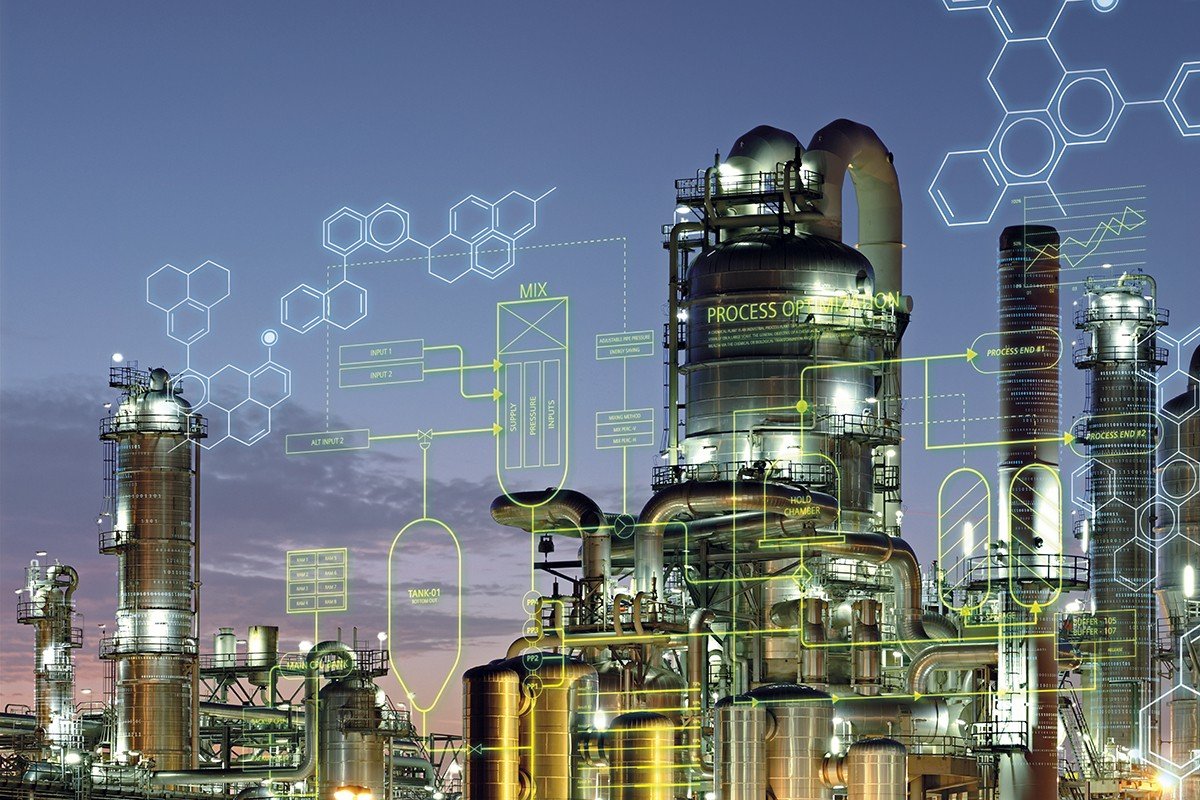
Geoptimaliseerde stoomroutes zorgden dat er minder stoom verloren ging. Een betere driver selectie resulteerde dan weer in een hogere efficiëntie. Kortom, een investering die meer dan de moeite waard was. De oplossing had zichzelf immers al na negen maanden terugverdiend. Maar ze loonde evenzeer voor het milieu met een bijkomende reductie in CO2-emissies van 3 tot 7%. Bovendien werden er in de eerste drie maanden extra besparingsmogelijkheden geïdentificeerd, goed voor 2,4 tot 5,6 miljoen euro op jaarbasis.
Future proof margarineproductie
Ook in food & beverage bewees Siemens zich al als de geknipte partner. Het ontwikkelde bijvoorbeeld een nieuw batch control systeem om de margarineproductie bij Vandemoortele aan te sturen. Voornaamste vereiste? Verticale integratie. Daarnaast stonden ook een automatische tracering in twee richtingen, een betere kwaliteitscontrole op de werkvloer, een beter zicht op de grondstofverbruiken in real time en een beter overzicht van de verschillende procesfasen voor de operatoren opgelijst in het lastenboek.
Concreet leverde Siemens een standaardoplossing met Simatic Batch en PCS 7 voor het aflopen van de receptstappen. Actemium – Siemens Solution Partner – stond daarbij als integrator in voor de programmatie, de visualisatie en een zekere customisatie, afgestemd op de installatie van Vandemoortele. Standaardoplossingen dus, wat maakt dat hetzelfde systeem zonder veel aanpassingen kan worden overgenomen in de margarinefabrieken in Barcelona en Dresden van dezelfde groep.
Breed portfolio, brede competenties
De rode draad in de keuze voor Siemens in deze projecten? “Duurzaamheid vertrekt vanuit digitalisering, dat geldt voor elke industrie. Het geeft je immers de mogelijkheid om kennis te borgen en te delen. Maar er komt zoveel meer bij kijken. Als Siemens hebben we alle technologie in huis, van de kleinste sensor om in het veld de metingen te doen, tot de meest complexe software om met behulp van artificiële intelligentie tot inzichten te komen. En daar voegen we dan de kennis van onze medewerkers aan toe. Want het draait om meer dan producten en systemen alleen, je moet efficiënte processen bouwen”, besluit Van Heurck.
siemens.be/industrie
Zelf het goede voorbeeld geven
Siemens neemt op vlak van duurzaamheid al vele jaren een pioniersrol op zich en versnelt voortdurend haar inzet. Met de publicatie van het duurzaamheidsrapport (ESG - Environmental, Societal and Corporate Governance) voor boekjaar 2022 kondigt de onderneming nieuwe, nog ambitieuzere doelstellingen aan voor de eigen decarbonisatie samen met uitgebreide investeringen.
- 46% CO2-reductie in de eigen bedrijfsactiviteiten sinds 2019
- Ambitieuze doelstellingen: 55% fysieke CO2-reductie tegen 2025 en 90% tegen 2030
- 150 miljoen ton emissies vermeden bij klanten dankzij Siemens producten en oplossingen verkocht in boekjaar 2022
- Investering van 650 miljoen euro voor de decarbonisatie van de eigen bedrijfsactiviteiten tegen 2030
- Investering van 280 miljoen voor opleiding en permanente vorming van het eigen personeel in boekjaar 2022